Desizers are Deciders
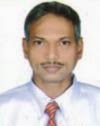
Dr. Ashok Athalye
G.M. Technical Service,
Atul Ltd (Colors Division), Valsad, Gujarat, India
Email: ashok_athalye@atul.co.in
Enzymes are widely used in the textile industry owing to their eco friendliness and suitability of application on different substrates under varying application conditions. The enzymes are now considered to be an integral part of almost every wet processing step of natural fibers, ranging from fabric preparation to the garment finishing. Enzymes are part of “White Biotechnology”, which is aimed at practicing environment friendly applications and using renewable resources.
The global market potential of enzymes for textile application is estimated to be about 150 mil USD having CAGR of about 3 %. The growth rate is envisaged to increase further depending on the changing fashions in “garment finishing” and the growing awareness of eco concerns demanding “Greener” processing. During the last decade many new applications have been developed and commercialized which has also expanded the market size considerably.
The major usage of enzymes in textile processing is in the areas of
- Desizing – of cotton woven fabrics, terry towels and denims
- Bioscouring – of cotton yarn & knits
- Biocleaning – degumming of Silk, Flax retting, decolorization of dye house waste water
- Biobleaching – of Wool
- Bleach clean-up – post bleaching peroxide neutralization
- Biopolishing – loose fiber, surface fuzz removal from knits/ towels for antipilling
- Biosoftening – soft finish on knits & garment, fading of denims
Basic facts on Enzymes :
The term ‘enzyme’ is derived from the Greek word enzume meaning “in (en) yeast (zume)”. The properties and reactions of Enzymes were first recognized by Kirchoff in 1811. It is considered that the first enzyme was purified and crystallized in 1926 by James Summer of Cornell University. Subsequent work by many researchers provides in-depth understanding of the structure, properties and classification of enzymes. The commercial applications of industrial enzymes range from detergents, textiles, leather and paper to animal feed, dairy, baking, brewing, distillery and protein hydrolysis.
Enzyme is a naturally occurring biological product produced by all living organism. It is composed of a complex 3 dimensional globular protein, comprising about 200 to 250 amino-acids having molecular weight as high as 104 – 105 and which are capable of catalyzing specific chemical reactions. Many enzymes also contain a non-protein component called “cofactor” for improved catalytic activity. Being catalysts of all reactions in the living system, the enzymes are also called as ‘bio-catalysts’. However, the enzyme catalysts differ from chemical catalysts in following important ways:
- Enzyme-catalyzed reactions are much faster than chemically-catalyzed reactions. Enzymes can enhance the reaction rates by 106 to 1013 times.
- Enzymes have greater reaction specificity and rarely form any by-products.
- Enzymes work under comparatively mild reaction conditions, such as temperatures below 1000C, atmospheric pressure and pH neither too acidic nor strongly alkaline.
- Very small amounts of enzymes are required to carry out chemical reactions and both solid and liquid enzyme preparations take up very little storage space.
- Mild operating conditions enable simple and widely available equipment to be used, and enzyme reactions are easily controlled and can be easily stopped as and when the desired degree of effect is achieved.
- Enzymes use significantly less water, energy, time for effective specific action, help control overall sustainability and reduce impact on carbon footprint.
Types of Enzymes
“Enzyme Commission” of the International Biochemical Union standardized a method of classification giving every enzyme an “EC number” with 4 digits.
Depending on the reaction methodology and the degree of specificity to catalyze a particular reaction, the Enzymes have been categorized into 6 classes.
- EC 1 - Oxido Reductase
- EC 2 – Transferase
- EC 3 - Hydrolase
- EC 4 – Lyase
- EC 5 - Isomerase
- EC 6 - Ligase
Most of the enzymes used in the textile industry belong to class 3 (hydrolase). The second number in the enzyme code, for hydrolases, describes the type of bond the enzyme hydrolyses and the third number further defines the reaction catalyzed. For example, an enzyme with the first two numbers 3.2. is a hydrolase that catalyses the hydrolysis of glycosidic bonds - bonds between carbohydrate residues in polymers such as starch and cellulose.
Mechanism of Enzyme Action
Chemical reactions proceed when the free energy of the products is less than that of the reactants. The speed of the chemical reactions depends on the energy barrier between the substrate and the product. This barrier is known as the ‘activation energy’ and for molecules to react, they must possess the energy to overcome the barrier.
However, enzymes do not increase the energy levels of substrate molecules, but provide an alternative low-energy route for the reaction to proceed. They achieve this by forming an intermediate enzyme-substrate complex, which alters the energy of the substrate such that it can be quite readily converted to the` product. The enzyme itself is released unaltered at the end of the reaction, thus acting as a catalyst.
It can be schematically represented by the following equation:
E + S → ES → E + P
(Initial state) (Intermediate state) (Final state)
Enzymes being highly specific catalysts, the substrate must fit precisely into the active site of the enzyme just like a key fitting into lock.
The formation of enzyme substrate complex also requires very little energy. Consequently, enzymes are very effective catalysts, enhancing reactions up to several thousand-fold more than the most effective chemical catalysts.
The substrate & reaction specificity is determined by the structure of enzyme. The primary structure is determined by the amino acid sequence, the secondary structure by the specific conformation of protein chain and the tertiary structure by the arrangement of chain segments.
![]() |
Above this value enzyme activity decreases rapidly until a point when the enzymes become permanently deactivated by denaturation. Temperatures below the optimum range decrease the enzyme activity without damaging the protein structure. Lower ranges of temperature can be used with longer times of exposure to the substrate.
The methods used in the textile industry to stop enzymatic reactions after the desired treatment is carried out are based on this characteristic. An increase in pH or temperature renders the enzymes inactive and harmless to the textile substrate.
![]() |
Enzymes being proteins, they are degraded by other proteolytic enzymes secreted by microorganisms present in sewerage plants to amino acids, which are then available to re enter the food chain.
Manufacturing of Enzyme
Generally, fermentation is done under strict control of pH, oxygen, feed additives, carbon dioxide, nutrients, minerals and substances which induce the production of the desired enzyme. It takes about 5-9 days for such fermentation to reach its peak (for maximum production level) then fermentation broth is filtered, concentrated and transformed into a storage stable product for commercial application. This can either be a liquid which has to be formulated to guarantee shelf life or supplied in powder form.
The molecular biologists are now able to manipulate such organisms so that the desired quality and quantity of the enzymes can be produced by either genetic engineering or protein engineering.
Biotechnology offers the possibility of producing enzymes for industrial use by optimizing the living conditions of a microorganism and, therefore, improving its “production capacity”.. After this fermentation process, the enzymes are isolated, and further processed for industrial use.
The general terminology used in enzyme manufacturing is given below
Term | Description |
Enzyme | Pure protein with a specified activity, on basis of which the enzyme is identified. The activity has an IUB and a CAS number. |
Enzyme concentrate | An enzyme-containing mixture in its most concentrated form as it occurs during commercial production, thus before formulation. Enzyme concentrates are not commercially available as such, but some may be used directly by the producer as a processing aid for food or to synthesize certain chemicals (i.e captive use). It is measured as Total Organic Substance (TOS). TOS = 100% - (Water +Ash +Diluents). |
Enzyme formulation | An enzyme concentrate, diluted to a standardised activity, stabilized and marketed for commercially application. |
Enzyme blend | A formulation of an intended mixture of enzyme concentrates originating from different sources. |
Declared enzyme | The enzyme component(s) in the preparation of significance in terms of application and regulation |
Enzymes are sensitive to the outside environment during their storage. Even a long storage period can affect the activity of an enzyme. With the change in activity level, the effectiveness of the enzyme will also change.
Enzymes in Textile Processing:
Enzymes have found wide application in the textile industry from fabric to garment finishing for improving efficiency of processing and enhancing aesthetic appeal.
Enzymes are used in the textile industry because they:
Enzyme activity is a measure of substrate molecules converted into product in a unit of time, per molecules of enzyme. In most instances specific activity is expressed as mole of substrate per min. (unit of enzyme activity) per mg of enzyme protein (U/mg protein).
Enzymes speed up a particular chemical reaction by lowering the activation energy for the reaction. They achieve this by forming an intermediate enzyme-substrate complex, which alters the energy of the substrate such that it can be more readily converted into the product. The enzyme itself is unaltered at the end of the reaction, thus acting as a catalyst.
The enzyme changes the reaction kinetics, allowing equilibrium to be reached much more rapidly. This is because the reaction of the enzyme with the substrate provides a new reaction pathway with lower transition state energy, thereby facilitating a more rapid conversion of substrate to product.
Besides these, enzymes differ from normal chemicals in some respects. One of them is, there is a difference between the activity of an enzyme and its concentration. The same level of enzyme can show different levels of activity, i.e., it can act faster or slower depending on conditions such as pH and temperature.
As the enzymes are very specific in action, as each type can affect only one chemical bond, more control over final effects is easily achieved. In terms of effluent, enzymes are quite clean and affect effluent only mildly, if at all. Many common chemicals used in textile manufacturing cause toxic products to be released in the effluent. Enzymes are even clean and ‘green’ to manufacture as well.
Depending on substrate specificity, the commonly used enzymes during textile processing are
Cotton is the most widely used natural cellulosic substrate. One of the processing steps involves sizing of yarn (coating of the warp threads by starch) in order to prevent their breakage during subsequent weaving. Generally, the sizing agents are selected depending on the quality of yarn and the fabric construction. The typical sizing agents used are natural starch (maize, potato, wheat, tapioca, rice, arrowroot, sago) and modified starch derivatives, polyvinyl alcohol (PVA), carboxy methyl cellulose (CMC), etc.
However, during the subsequent process this applied size (surface coating on yarn) has to be removed from woven fabric for further wet processing comprising bleaching, dyeing, printing and finishing. The removal of starch from yarn surface is termed as ‘desizing’.
The purpose of desizing is to adequately remove enough of the size film to allow further wet processing steps to occur at optimum efficiency. Thus, desizing is considered to be a key parameter which determines performance of further processing.
Enzymes in Textile Processing:
Enzymes have found wide application in the textile industry from fabric to garment finishing for improving efficiency of processing and enhancing aesthetic appeal.
Enzymes are used in the textile industry because they:
- Act only on specific substrates
- Can replace harsh chemicals
- Operate under mild conditions
- Accelerate reactions
- Are safe and easy to control
- Are biodegradable
Enzyme activity is a measure of substrate molecules converted into product in a unit of time, per molecules of enzyme. In most instances specific activity is expressed as mole of substrate per min. (unit of enzyme activity) per mg of enzyme protein (U/mg protein).
Enzymes speed up a particular chemical reaction by lowering the activation energy for the reaction. They achieve this by forming an intermediate enzyme-substrate complex, which alters the energy of the substrate such that it can be more readily converted into the product. The enzyme itself is unaltered at the end of the reaction, thus acting as a catalyst.
The enzyme changes the reaction kinetics, allowing equilibrium to be reached much more rapidly. This is because the reaction of the enzyme with the substrate provides a new reaction pathway with lower transition state energy, thereby facilitating a more rapid conversion of substrate to product.
Besides these, enzymes differ from normal chemicals in some respects. One of them is, there is a difference between the activity of an enzyme and its concentration. The same level of enzyme can show different levels of activity, i.e., it can act faster or slower depending on conditions such as pH and temperature.
As the enzymes are very specific in action, as each type can affect only one chemical bond, more control over final effects is easily achieved. In terms of effluent, enzymes are quite clean and affect effluent only mildly, if at all. Many common chemicals used in textile manufacturing cause toxic products to be released in the effluent. Enzymes are even clean and ‘green’ to manufacture as well.
Depending on substrate specificity, the commonly used enzymes during textile processing are
- Amylases - for Starch
- Cellulases - for Cellulose
- Catalases - for Hydrogen Peroxide
- Pectinases - for Pectins
- Proteases - for Proteins
Cotton is the most widely used natural cellulosic substrate. One of the processing steps involves sizing of yarn (coating of the warp threads by starch) in order to prevent their breakage during subsequent weaving. Generally, the sizing agents are selected depending on the quality of yarn and the fabric construction. The typical sizing agents used are natural starch (maize, potato, wheat, tapioca, rice, arrowroot, sago) and modified starch derivatives, polyvinyl alcohol (PVA), carboxy methyl cellulose (CMC), etc.
However, during the subsequent process this applied size (surface coating on yarn) has to be removed from woven fabric for further wet processing comprising bleaching, dyeing, printing and finishing. The removal of starch from yarn surface is termed as ‘desizing’.
The purpose of desizing is to adequately remove enough of the size film to allow further wet processing steps to occur at optimum efficiency. Thus, desizing is considered to be a key parameter which determines performance of further processing.
Type of Size | Advantages | Disadvantages | Method of Desizing |
Starch | low cost, safe to use, biodegradable, easy to detect, stable to high humidity | forms skins, high viscosity, non recyclable | enzymes (amylases) or oxidative chemicals |
Modified starch | soluble in water, easier to remove, lower viscosity, no skin formation | more expensive than starch, lower biodegradability, non recyclable | enzymes (amylases) or hot washing |
Carboxy methyl cellulose (CMC) | good film formation, no skin formation | with salts is corrosive, may precipitate, re-swells in desizing bath, poor biodegradability, sticky marks at high humidity | hot detergent wash |
polyvinyl alcohol (PVA) | good weaving performance, readily combines with other sizes, elastic films, stable against humidity | sensitive to alkalis, forms skins, foams, slow solubility, sensitive to singeing, poor biodegradability | hot detergent wash |
Triglyceride | increased flexibility and weaving yield, prevents dry-splitting of size | problems if not properly removed: uneven dye uptake, reduced colour | enzyme treatment (lipase) |
Although many different compounds have been used to size fabrics over the years, starch has been the most common sizing agent for more than a century and this is still the case today.
The 3 major areas involving desizing as an important processing step in apparel and home textiles are
Although the specific action of amylases for starch splitting was known earlier, the industrial scale enzymatic desizing was commercialized in the late 1960s.
Starch comprises a mixture of a linear polymer and a branched polymer. Amylose is a flexible linear polymer of glucose residues joined by alpha-1,4 glycosidic bond (Figure 1), which may be formed from several thousand glucose molecules. Amylopectin, however, is a branched molecule of glucose residues joined by either the alpha-1,4 or alpha-1,6 glycosidic bond. The proportion of the two polymers, amylose and amylopectin, depends upon the source of starch. Starch from wheat, for example, contains approximately 25% amylose and 75% amylopectin.
The product used for hydrolysis and modification of the starch polymer requires a combination of enzymes for its complete hydrolysis, which include alpha-amylases, beta-amylases and iso-amylases. These are further classified into endo-acting and exo-acting enzymes. Alpha-amylase is an endo-acting and hydrolyses linkages in a random fashion and leads to the formation of linear and branched oligosaccharides, while the rest are exo-acting enzymes and attack the substrate from non-reducing end, producing oligo and/or mono saccharides.
The enzymes alpha-amylases hydrolyse starch in an ‘endo’ fashion, cleaving at random internal alpha-1,4 glycosidic bonds in both amylose and amylopectin, showing little or no activity on the alpha-1,6 bonds. These enzymes degrade starch to shorter polymeric fragments, known as dextrins and maltose, a disaccharide, which contain two glucose residues. Alpha-amylases are found in microorganisms, plants and animals. alpha-amylases are relatively small proteins, of molecular weight between 50-60 k daltons.
The pH and temperature optima of the alpha-amylases depends upon the origin of the enzyme and these properties influence which enzymes will be of value in a particular industrial process. The temperature optimum of amylases from Bacillus licheniformis is 90 ºC and about 70 ºC for B. subtilis. Alpha-amylases generally have a pH optimum between 6 to 7. Being metalo-enzymes, alpha-amylases require the presence of calcium to increase its activity and stability.
Certain salts increase the activity of specific enzymes. Pancreatic amylase is ineffective without the addition of salt. A combination of sodium chloride and calcium chloride increases the stability of bacterial amylase.
Desizing a Critical Process
Desizing is done in order to remove the size from the warp yarns of the woven fabrics. The residual size on the warp yarns can resist subsequently applied dyes and chemicals, therefore, it needs to be removed before any subsequent wet processing of the fabric. The factors, on which the efficiency of size removal depends, are as follows:
Depending on the type of substrate (woven fabric, terry towel, denim/garment) and the machinery in use (jigger, soft flow/winch, drum washer, pad-batch, pad-steam), desizing operation is performed by exhaust, semi continuous or continuous application methods.
Desizing on a jigger is a simple method where the fabric from one roll is processed in a bath and rewound on another roll. First, the sized fabric is washed in hot water (80-95°C) to gelatinize the starch. The desizing liquor is then adjusted to pH 5.5-7.5 and a temperature of 60-80°C depending on the enzyme. The amylase is added in an impregnation stage and degraded starch in the form of dextrins is then removed by washing at 90-95°C for two minutes. The jigger process is a batch process. In contrast, in modern continuous high-speed processes, the reaction time for the enzyme may be as little as 15 seconds.
Desizing on pad rolls is continuous in terms of the passage of the fabric. However, a holding time of 2-16 hours at 20-60°C is required using low-temperature alpha-amylases before the size is removed in washing chambers. With high-temperature amylases, desizing reactions can be performed in steam chambers at 95-100°C or even higher temperatures to allow a fully continuous process.
Also, it is imperative to note some of the limitations of enzymatic desizing include lower additional cleaning effect towards other impurities, no effect on certain starches (e.g. tapioca starch) and possible loss of effectiveness through chemicals which act as enzyme deactivators or poisons.
Inadequate desizing will lead to problem in subsequent wet processing
The 3 major areas involving desizing as an important processing step in apparel and home textiles are
- Woven fabrics
- Denims and garments
- Terry towels
![]() |
Starch comprises a mixture of a linear polymer and a branched polymer. Amylose is a flexible linear polymer of glucose residues joined by alpha-1,4 glycosidic bond (Figure 1), which may be formed from several thousand glucose molecules. Amylopectin, however, is a branched molecule of glucose residues joined by either the alpha-1,4 or alpha-1,6 glycosidic bond. The proportion of the two polymers, amylose and amylopectin, depends upon the source of starch. Starch from wheat, for example, contains approximately 25% amylose and 75% amylopectin.
The product used for hydrolysis and modification of the starch polymer requires a combination of enzymes for its complete hydrolysis, which include alpha-amylases, beta-amylases and iso-amylases. These are further classified into endo-acting and exo-acting enzymes. Alpha-amylase is an endo-acting and hydrolyses linkages in a random fashion and leads to the formation of linear and branched oligosaccharides, while the rest are exo-acting enzymes and attack the substrate from non-reducing end, producing oligo and/or mono saccharides.
The enzymes alpha-amylases hydrolyse starch in an ‘endo’ fashion, cleaving at random internal alpha-1,4 glycosidic bonds in both amylose and amylopectin, showing little or no activity on the alpha-1,6 bonds. These enzymes degrade starch to shorter polymeric fragments, known as dextrins and maltose, a disaccharide, which contain two glucose residues. Alpha-amylases are found in microorganisms, plants and animals. alpha-amylases are relatively small proteins, of molecular weight between 50-60 k daltons.
The pH and temperature optima of the alpha-amylases depends upon the origin of the enzyme and these properties influence which enzymes will be of value in a particular industrial process. The temperature optimum of amylases from Bacillus licheniformis is 90 ºC and about 70 ºC for B. subtilis. Alpha-amylases generally have a pH optimum between 6 to 7. Being metalo-enzymes, alpha-amylases require the presence of calcium to increase its activity and stability.
Certain salts increase the activity of specific enzymes. Pancreatic amylase is ineffective without the addition of salt. A combination of sodium chloride and calcium chloride increases the stability of bacterial amylase.
![]() |
Desizing is done in order to remove the size from the warp yarns of the woven fabrics. The residual size on the warp yarns can resist subsequently applied dyes and chemicals, therefore, it needs to be removed before any subsequent wet processing of the fabric. The factors, on which the efficiency of size removal depends, are as follows:
- Type and amount of size applied
- Viscosity of the size in solution
- Ease of dissolution of the size film on the yarn
- Nature and the amount of the plasticizers in the size film
- Fabric construction
- Method of desizing, and
- Method of washing-off
- Effective solubilization and removal of starches
- Excellent biodegradability
- No aggressive chemicals needed, thus maintaining the tensile strength of the substrate
- Safe handling and operation
- Improved wettability
- Improved fabric quality
- Reproducible performance and ease of use
- Amylase enzyme
- pH stabiliser
- Chelating agent
- Salt
- Surfactant
Depending on the type of substrate (woven fabric, terry towel, denim/garment) and the machinery in use (jigger, soft flow/winch, drum washer, pad-batch, pad-steam), desizing operation is performed by exhaust, semi continuous or continuous application methods.
Desizing on a jigger is a simple method where the fabric from one roll is processed in a bath and rewound on another roll. First, the sized fabric is washed in hot water (80-95°C) to gelatinize the starch. The desizing liquor is then adjusted to pH 5.5-7.5 and a temperature of 60-80°C depending on the enzyme. The amylase is added in an impregnation stage and degraded starch in the form of dextrins is then removed by washing at 90-95°C for two minutes. The jigger process is a batch process. In contrast, in modern continuous high-speed processes, the reaction time for the enzyme may be as little as 15 seconds.
Desizing on pad rolls is continuous in terms of the passage of the fabric. However, a holding time of 2-16 hours at 20-60°C is required using low-temperature alpha-amylases before the size is removed in washing chambers. With high-temperature amylases, desizing reactions can be performed in steam chambers at 95-100°C or even higher temperatures to allow a fully continuous process.
Also, it is imperative to note some of the limitations of enzymatic desizing include lower additional cleaning effect towards other impurities, no effect on certain starches (e.g. tapioca starch) and possible loss of effectiveness through chemicals which act as enzyme deactivators or poisons.
Inadequate desizing will lead to problem in subsequent wet processing
- Reduced absorbency
- Inadequate whiteness
- Paler dyeing
- Spotty dyeing
- Reserved marks in dyeing and printings
- Increased tendency to creasing due to hard handle
- Reduced tear strength
Symptoms | Diagnosis | Cure |
Incomplete desizing |
|
|
Uneven desizing [width ways] |
|
|
Uneven desizing [length ways] |
|
|
Uneven desizing [random] |
|
|
After desizing, the fabric should be systematically analyzed to determine the uniformity, effectiveness and thoroughness of the treatment. The commonly used test methods are
Ideally, after desizing, residual size should not be more than 1% owf. A drop of dilute iodine solution (I2 in KI) is placed on the fabric and the color change observed and assessed by TEGEWA scale. The fabric is not spotted randomly but from side-centre-side at different points along the length of the fabric. A dark bluish violet color indicates excessive starch and if so, the fabric or garments must be reprocessed.
Another method of determination of efficacy of enzyme is by assessing its specific activity in stated units. One unit is the amount of enzyme which will hydrolyse one µmole of substrate per minute under given conditions of pH, buffer composition. However, the test methods and the units of measurements vary with different manufacturers and formulators (though the international standard is KATAL unit).
Factors affecting Enzyme activity :
Summary :
Sizing is necessary to ensure that yarns are adequately protected during weaving as the modern looms operate at very high speeds, causing excessively high abrasion to the yarn. Starch is the preferred sizing agent for cotton and blends. To ensure that fabric is well prepared for dyeing and further processing, all size must be removed adequately and uniformly. Failure to remove the size ingredients can result in poor absorbency, uneven dyeing, poor batch-to-batch shade reproducibility, improper printing and inadequate finishing resulting in poor fabric hand feel. Thus, enzymatic desizers are deciders of effective fabric processing.
- Assessment of weight loss
- TEGEWA scale rating
- Water, color solution absorbency
- Hand feel
- Bending length
- Effect on tensile and tear strength
Ideally, after desizing, residual size should not be more than 1% owf. A drop of dilute iodine solution (I2 in KI) is placed on the fabric and the color change observed and assessed by TEGEWA scale. The fabric is not spotted randomly but from side-centre-side at different points along the length of the fabric. A dark bluish violet color indicates excessive starch and if so, the fabric or garments must be reprocessed.
Another method of determination of efficacy of enzyme is by assessing its specific activity in stated units. One unit is the amount of enzyme which will hydrolyse one µmole of substrate per minute under given conditions of pH, buffer composition. However, the test methods and the units of measurements vary with different manufacturers and formulators (though the international standard is KATAL unit).
Factors affecting Enzyme activity :
- Substrate concentration - the rate of enzyme activity increases with substrate conc. at lower level upto a certain point and then slows down.
- pH value – the amino acids and other ionisable groups in enzyme may get ionized at lower or higher pH effecting its activity.
- Temperature – with increase in temp the reaction rate increases due to “thermal energy”, but with further increase in temp the rate decreases due to thermal denaturation.
- Activators – presence of specific bivalent metal cation can activate enzyme reaction. Such metal ions stabilize the structure of enzyme-substrate complex or sensitize the substrate to the attack of enzyme or take part in the ion exchange process.
- Inhibitors – certain alkalis, acids and antiseptic tend to inhibit enzyme activity.
- Reducing sugar release
- Colorimetric assays
- Viscometric assays
- Immunological methods
- Gel Diffusion methods
Summary :
Sizing is necessary to ensure that yarns are adequately protected during weaving as the modern looms operate at very high speeds, causing excessively high abrasion to the yarn. Starch is the preferred sizing agent for cotton and blends. To ensure that fabric is well prepared for dyeing and further processing, all size must be removed adequately and uniformly. Failure to remove the size ingredients can result in poor absorbency, uneven dyeing, poor batch-to-batch shade reproducibility, improper printing and inadequate finishing resulting in poor fabric hand feel. Thus, enzymatic desizers are deciders of effective fabric processing.
{ 0 comments... read them below or add one }
Post a Comment